Zero failure tolerance is our constant.
Get a better view into our in-house, aircraft quality, custom offering and process.
3D Printing
We're pleased to announce that we have take delivery of a Makerbot Replicator Z18 3D Printer. Our 3D printer allows us to 3D print 12`` x 12`` x 18``. Using filament, this 3D printer will be helpful to our clients, including:
Aerospace Quality
Our precision parts – and the processes behind them – are built to meet aerospace industry specifications and standards. At DP Cast, process control is paramount, resulting in more value-added products and services for our customers.
Excellent Mechanical Properties
Working closely with leading clients in aerospace — an industry requiring high-integrity components — we’ve systematically applied our proprietary fill-control system, known as Functional Counter GravityTM, to help eliminate the sources of mechanical property variations that can lead to major fatigue in safety–critical parts. As a result, we now offer complex, precision components with enhanced physical properties to suit your specifications. Click here to learn more.
Aerospace
In September of 2017, our facility in Brampton, Ontario was awarded independent ISO 9001:2015 and AS 9100D Certification by the prestigious Bureau Veritas. A management system certified by Bureau Veritas certification is recognized worldwide as a symbol of excellence. While our precision parts – and the processes behind them – have always been built to meet stringent aerospace industry specifications, this milestone places DP Cast among an elite group of companies that adhere to established international quality standards, as a sign of our Company’s commitment to quality. The distinction of this awarded certification underscores DP Cast’s ongoing focus on professional business practices, consistent results, process controls and continuous improvement throughout all stages of parts development, product assistance, production and delivery – meeting industry demand and exceeding ever-growing client expectations for the highest level of quality.
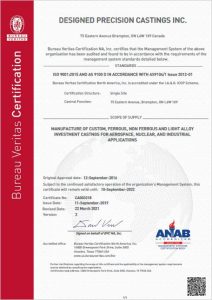
ISO9001:2015 and AS9100D Certification
Mold Making
Our in-house mold-making facilities result in a quality mold, delivered in a timely manner under DP Cast’s direct control CNC machining centre, combined with Solidworks and Surfcam 3D software allows us to accept your computer file electronically for manufacture. No matter your requirement, at DP Cast, we have the ability to maintain, repair and modify your molds as required.
Product Assistance
At DP Cast, we don’t just execute your design – we influence it through applied engineering, prototyping, tooling, thorough review, testing and build innovation. Our involvement during the concept stage allows us to identify ways to reduce time and post processing costs, such as machining, fabrications and weldings, resulting in a higher-quality part.
Part Optimization
Investment casting allows for fabrications involving the joining of two or more parts to be cast as one piece, saving clients both time and money. Moreover, the elimination of expensive turning, milling, welding, drilling, etc. can, in certain cases, eliminate the need for all finishing.

Non-Destructive Testing
An audited supplier to the aerospace industry, DP Cast provides comprehensive, non-destructive testing (and non-destructive testing at source), with Level III, CGSB, ASNTSNT-TC-1A and NAS410-certified personnel, equipment and facilities, to all of our customers, regardless of sector in the following methods:
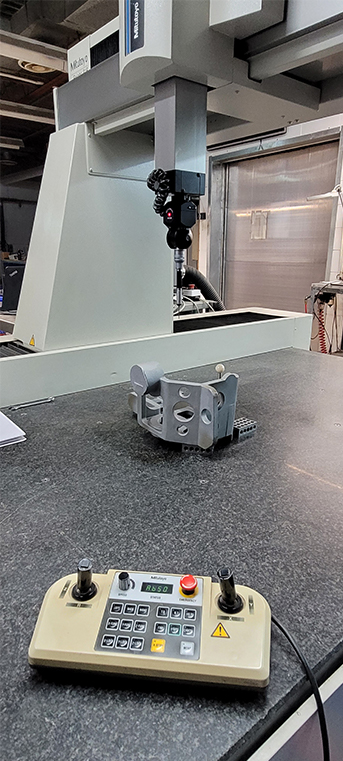
Melt & Pour
All of our castings are produced onsite from molds made at our facilities in Brampton, Canada and poured from our 5 melt furnaces:
Quality Assurance
DP Cast’s quality assurance personnel are delegated and approved by Aerospace OEM’s to act on their behalf as quality representatives. Our facility features a comprehensive Preventative Maintenance Program, as well as a Measuring and Test Equipment Control Program, and 3D surface profile measurement and dimensional inspection capabilities through Coordinate Measurement Machine (CMM) Metrology to verify part dimensions. We can supply testing and laboratory services, including chemical analysis (spectrographic and metallurgical) and mechanical testing for tensile and hardness, traceable to American NIST standards to verify as cast and heat treated conditions of castings. DP Cast is Qualified as a Laboratory Control at Source and Non-Destructive Testing at Source provider for select clients.
Alloys
At DP Cast we pour a wide range of alloys:
Alloy | UNS | Specification | Condition | Ultimate Tensile Strength Min KSI | Yield Strength Min KSI | Elongation % | Remarks | |
---|---|---|---|---|---|---|---|---|
1020 | ASTM-A-732 1A/ASTM A216 WCA | Normalize & Temper | Low Alloy Steels | |||||
1025 | ASTMA 216 WCB | Normalize & Temper | Low Alloy Steels | |||||
1030 | ASTM-A-732 | Quench & Temper | 75 | 48 | 25 | Harder carbon steel | Low Alloy Steels | |
1040 | ASTM-A-732 | Quench & Temper | Low Alloy Steels | |||||
1045 | ASTM A487 DN | Quench & Temper | Low Alloy Steels | |||||
1050 | ASTM-A-732 4A/4Q | Quench & Temper | Low Alloy Steels | |||||
4130 | ASTM-A-732 7Q/AMS 5336 | Quench & Temper | 180 | 145 | 5 | Strong, hard, wear and fatigue- resistant | Low Alloy Steels | |
4140 | ASTM-A-732, A958 | Quench & Temper | Low Alloy Steels | |||||
4340 | ASTM-A-732 10Q/AMS 5330 | Quench & Temper | Low Alloy Steels | |||||
4615 | ASTM-A-732 | Quench & Temper | 190 | 170 | 4 | Hard and strong | Low Alloy Steels | |
6150 | ASTM-A-732 12Q | Quench & Temper | 105 | 85 | 10 | Good blend of properties | Low Alloy Steels | |
8620 | ASTM-A-732 13Q/AMS-S22141 | Quench & Temper | Low Alloy Steels | |||||
8630 | ASTM A732 14Q/AMS5334 | Quench & Temper | Low Alloy Steels | |||||
8640 | AMS-S-22141 | Quench & Temper | Low Alloy Steels | |||||
9310 | Case Hardening Steel | Low Alloy Steels | ||||||
52100 | ASTM A732 15A | Normalize & Quench | Bearing Steel | Low Alloy Steels | ||||
A2 | CA-2 | ASTM A-597 | Annealed/Quench & Temper | Tool Steels | ||||
D2 | CD-2 | ASTM A-597 | Annealed/Quench & Temper | Tool Steels | ||||
O1 | CO-1 | ASTM A-597 | Annealed/Quench & Temper | Tool Steels | ||||
C5 | CS-5 | ASTM A-597 | Annealed/Quench & Temper | Tool Steels | ||||
H13 | CH13 | ASTM A597 | Anneal/Quench & Temper | Tool Steels | ||||
303 | CF16 | ASTM A351, A743, A744, AMS 5370/1 | As cast/Solution annealed for improved corrosion resistance | 70 | 30 | 35 | Stainless (Austenitic) Steels | |
304 | CF8 | ASTM A351, A743, A744 | As cast/Solution annealed for improved corrosion resistance | 70 | 30 | 35 | Stainless (Austenitic) Steels | |
304L | CF3 | ASTM A351, A743 | As cast/Solution annealed for improved corrosion resistance | Low Carbon | Stainless (Austenitic) Steels | |||
309 | GH20 | ASTM A351, A743 | As cast/Solution annealed for improved corrosion resistance | Stainless (Austenitic) Steels | ||||
310 | CK20 | ASTM A351, A743, A744, AMS 5365/66 | As cast/Solution annealed for improved corrosion resistance | 70 | 30 | 30 | Molybdenum Modified | Stainless (Austenitic) Steels |
316 | CF8M | ASTM A351, A743, A744/MIL-S-81591 | As cast/Solution annealed for improved corrosion resistance | 70 | 30 | 30 | Stainless (Austenitic) Steels | |
316L | CF3M | ASTM A351, A743, A744 | As cast/Solution annealed for improved corrosion resistance | Low Carbon | Stainless (Austenitic) Steels | |||
317 | CG8M | ASTM A351, A743, A744 | As cast/Solution annealed for improved corrosion resistance | Stainless (Austenitic) Steels | ||||
321 | MIL-S-81591 | As Cast/Solution annealed for improved corrosion resistance | 70 | 30 | 30 | Stainless (Austenitic) Steels | ||
347 | CF8C | ASTM A351 743/AMS 5362/5364 | Solution Annealed | Niobium Modified | Stainless (Austenitic) Steels | |||
Alloy 20 | CN7M | ASTM A351, A743, A744 | As Cast/Solution annealed for improved corrosion resistance | Stainless (Austenitic) Steels | ||||
410 | ASTM A743 A217/AMS 5350 | Harden & Temper | 95 | 75 | 8 | Chromium (Martensitic) Steels | ||
416 | AMS 4349 | Harden & Temper | 95 | 65 | 8 | Chromium (Martensitic) Steels | ||
420 | CA40 | ASTM A743 | Harden & Temper | Chromium (Martensitic) Steels | ||||
436 (Greek Ascoloy) | AMS 5352, MIL-S-81591 | Homogenize/Austenatize & Temper | 145 | 115 | 10 | Chromium (Martensitic) Steels | ||
440C | ASTM A-743/AMS 5352 | Annealed/Harden & Temper | Chromium (Martensitic) Steels | |||||
442 | CB30 | ASTM A-743 | Annealed/Harden & Temper | 175 | 150 | 5 | Chromium (Martensitic) Steels | |
15-5PH | CB7Cu-2 | ASTM A747/AMS 5347/56/57 | Solution Anneal & Precipitation Harden | 90 | 65 | 18 | Precipitation Hardening Stainless Steels | |
17-4PH | CB&CU-1 | ASTM A747/AMS 5342/43/44/55 | Homogenize/Solution anneal & Precipitation Harden | 180 | 160 | 6 | Precipitation Hardening Stainless Steels | |
C355 | AMS 4215, ASTM B-618/B26 | T6 | 37 | 30 | 1 | Aluminum Alloys | ||
C356 | AMS 4260 ASTM B616/B26 | T6 | 33 | 22 | 3 | Aluminum Alloys | ||
F357 | AMS 4289 | T6 | 41 | 32 | 3 | Aluminum Alloys | ||
85-5-5-5 | C836 | ASTM B584 | Copper Alloys | |||||
MnBronze | C863 | ASTM B584 | Copper Alloys | |||||
SiBrass | C873/4 | ASTM B584 | Copper Alloys | |||||
SiBronze | C876 | ASTM B584 | Copper Alloys | |||||
Cobalt 6 | AMS 5387 | As Cast | Hardness HRC37 min. | Cobalt Alloys | ||||
Cobalt 12 | AMS 5382 | As Cast | Cobalt Alloys | |||||
Alloy 31 | AMS 5382 | As Cast | Cobalt Alloys | |||||
Alloy 400 | MONEL M30-C (N24130) | ASTM A494 | Solution annealed | Nickel Alloys | ||||
Alloy 411 | N-12MV | ASTM A494 | Solution annealed | Nickel Alloys | ||||
Hastelloy B | N-7M (N30007) | ASTM A494 | Solution annealed | Nickel Alloys | ||||
Inconel 600 | CY40 | ASTM A494 | Solution annealed | Nickel Alloys | ||||
Inconel 625 | CW6MC | AMS 5599/ASTM A494 | Solution annealed | Nickel Alloys | ||||
Hastelloy C mod | CW-2M (N26455) | ASTM A494 | Solution annealed | Nickel Alloys |
Engineering
Our engineering development team uses the latest hardware and software tools to ensure the casting process produces acceptable metallurgical and dimensional characteristics that meet all drawing, design and specification requirements: